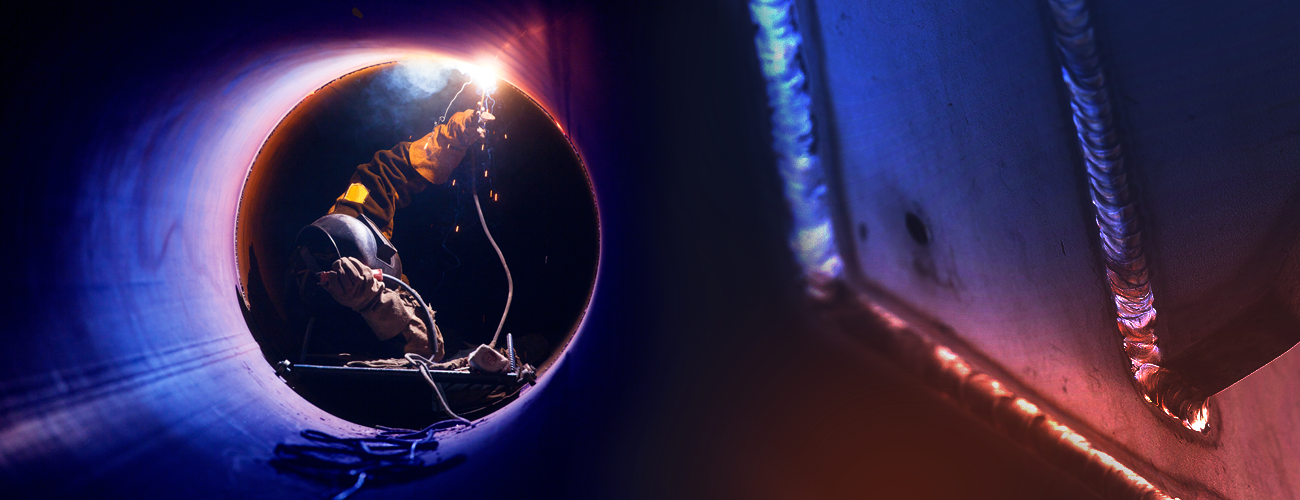
Concepts of holistic weld seam evaluation
Welded joints are suitable as permanent, non-detachable connections in construction, especially when flexibility and weight savings are required compared to other types of connection. However, if improperly designed and manufactured, the weld seam can represent a weak point in the component and lead to costly repairs or accidents. It is therefore important to carry out a careful weld assessment in advance to ensure the structural integrity and safety of structures. Weld calculation and assessment is primarily an engineering discipline and requires a deep understanding of (continuum) mechanics, material science, the design and the load cases in service.
Holistic view of weldability
As a rule, the geometry and the material of the weld seam are decisive for assessing the load-bearing capacity; other welding parameters and the choice of welding process only play a subordinate role according to current standards. A holistic consideration of weldability in accordance with the requirements of the welding triangle is mandatory in order to avoid subsequent damage.

depending on the type of load and stress and depending on the geometry and the standard / set of rules to be used, different concepts can be used to assess the load-bearing capacity of weld seams.
Weld evaluation methods
There are different methods for evaluating a weld seam. In general, three concepts are distinguished, which in turn can be subdivided into further sub-concepts:
- Nominal voltage concept
- Structural stress concept
- Notch stress concept
All concepts can be used to evaluate structures under both static and fatigue loads, whereby each concept has its advantages and disadvantages.
What all methods have in common is that reliable knowledge of the prevailing stress in the structure must be available. This can be determined, for example, by converting strain gauges measured on the real component or globally by using the finite element method (FEM). The FEM offers the advantage that no real structure is required and geometry and material variations can be easily investigated.
The nominal stress concept is based on an analytical approach, which is why it is primarily intended for simple geometries. A force acting on a reference cross-section results in a nominal stress. Simple geometries can thus be quickly recalculated by hand; MDESIGN weld provides support for the preliminary design.
However, by using FEM-based tools in post-processing, weld seams can be evaluated very accurately on a section-by-section basis. In industries with relatively thin-walled structures, such as shipbuilding, this is the most frequently used method, as the model structure in the FEM is often realized using shell elements.
The nominal stress concept reaches its limits with local effects, such as those that can occur at the end of the weld seam. These are often not or only insufficiently detectable. Complex geometries and three-dimensional stress states can also no longer be meaningfully evaluated using this approach.
With the structural stress concept , weld seams are represented in a simplified form in the FE model. With this method, unrealistically high stresses are often calculated at the weld seam transitions and/or the root, which are eliminated by applying various concepts. The best known methods are: Hot-spot method, CAB and internal linearization. The structural stress concept is particularly suitable for the investigation of rather three-dimensional / volumetric structures with complex weld seams.
The notch stress concept allows the targeted investigation of critical points. This method is often used following one of the above-mentioned concepts in order to gain a detailed insight into the stress states of the weld seam. The weld seam geometry is modeled close to the real state, the weld seam transition and the weld seam root are rounded with a defined radius and calculated. The stresses can be used directly for the evaluation.
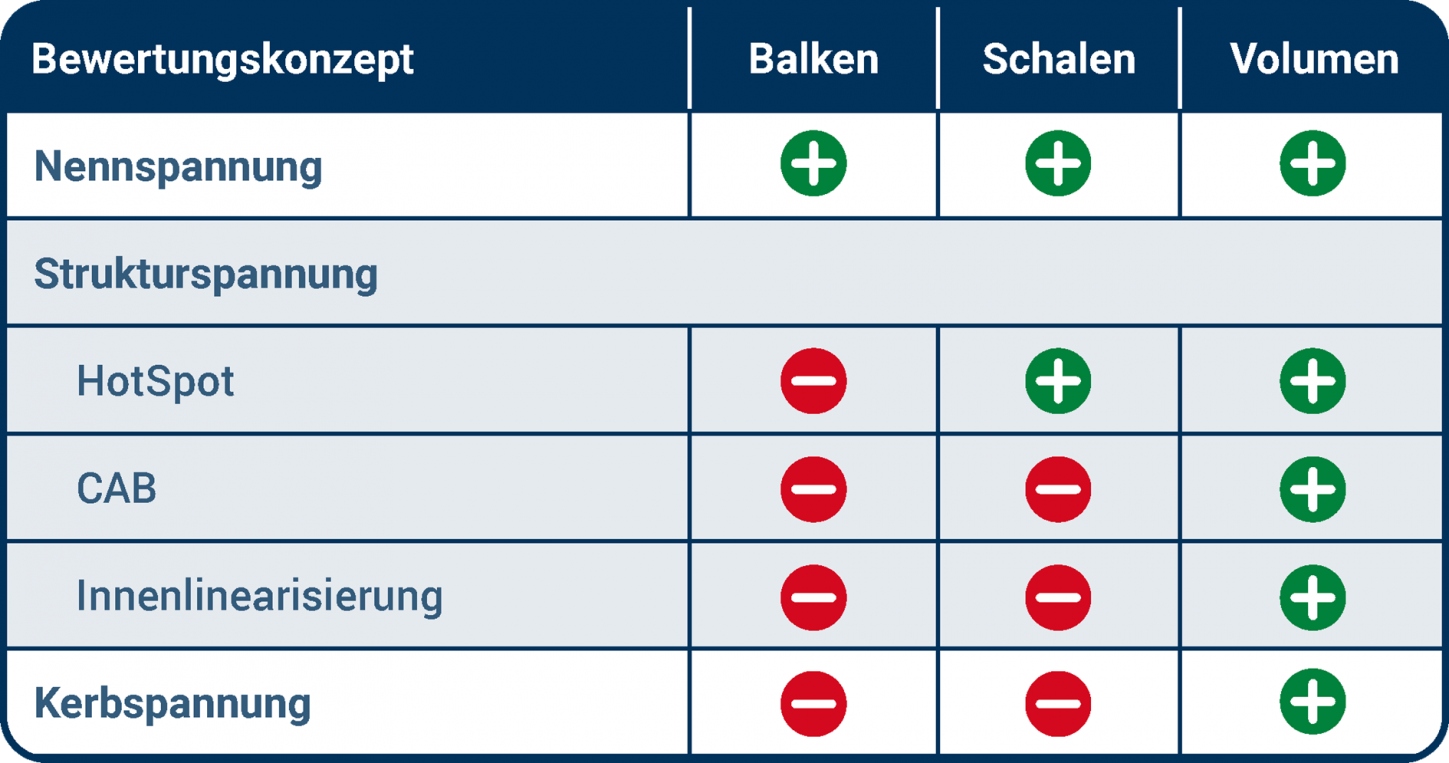
The MDESIGN calculation module "Component strength verification, FKM" offers you the option of determining the load-bearing capacity of a welded component with known local stresses using the notch or structural stress concept via the FKM guideline.
Selection of the appropriate method depends on the application
The choice of a suitable assessment method depends on many factors. In general, the effort and complexity increase with the level of detail of the assessment method (from the nominal stress concept to the structural stress concept to the notch stress concept).
The shell model in the nominal stress concept is suitable for investigating large, thin-walled structures. This method also provides fast and meaningful results in the concept phase, when wall thicknesses and weld seam types are often not yet defined.
For volumetric components, however, the structural stress concept with one of the sub-methods (hot-spot, CAB and internal linearization) is suitable. It is also possible to combine several of these sub-methods to cover all evaluation points.
The notch stress model is suitable for detailed investigations. Although this method is more complex, it allows the actual geometry to be taken into account. Particularly in the case of damage in the weld seam, the outer weld seam geometry (if intact) can be recorded by optical measurement and transferred to the finite element model. This allows the notch stresses to be determined, taking into account the surface properties and seam transitions.
No clear recommendation for or against a specific method can be given. The choice depends heavily on the design status (concept, elaboration, testable strength verification) and the underlying standard (e.g. Eurocode, FKM, DVS 1612 etc.). In principle, a holistic approach in the sense of the welding triangle (see above) should be followed for dimensioning, calculation, evaluation and implementation on the real component.
Digital help with the evaluation of weld seams
The most important verification methods for the calculation of weld seams can be found in MDESIGN weld. Use the intuitive support provided by MDESIGN to verify the load-bearing capacity of your weld seam design using one of the following calculation bases:
- Instruction sheet DVS 0705
- Instruction sheet DVS 1612
- Eurocode 3
- FKM guideline
Some results of the weld seam calculation are displayed in 2D models, which allows a quick, visual evaluation. Furthermore, MDESIGN weld offers access to all relevant material characteristics of the four available load-bearing capacity verifications through the implemented databases. While DVS 1612 and Eurocode 3 severely limit the choice of materials on the verification side, you can fall back on the material characteristics of the FKM guideline for a verification in accordance with DVS 0705 and the FKM guideline.
This means that not only numerous steels suitable for welding are available to you, but also aluminum materials.
MDESIGN offers further support with the "Component strength verification, FKM" calculation module: It allows you to check the load-bearing capacity of complex weld seam geometries with known local stresses using the notch or structural stress concept. MDESIGN therefore provides you with a wide range of verification methods for weld seam load-bearing capacity.
Seminar tip:The MDESIGN knowledge update online seminar "Application and method differences in weld seam calculation" provides detailed knowledge about verification concepts for the calculation of weld seams and their areas of application.