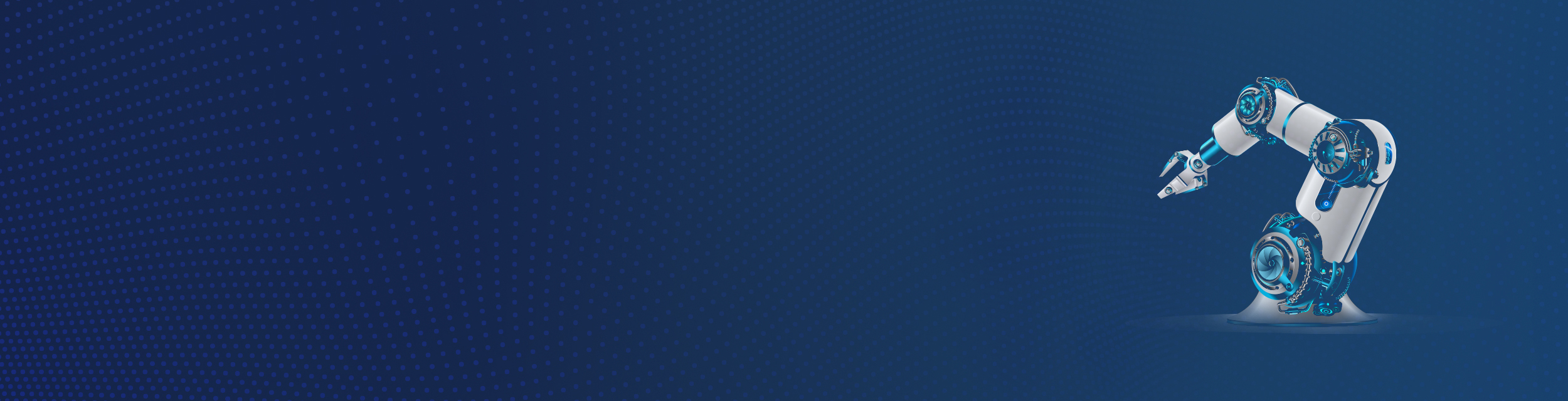
A quality product with AI support
Intelligent manufacturing
Using AI for optimization
The application of machine learning in mechanical engineering can help to optimize production processes. By using machine learning methods to evaluate production deviations, efficiency can be increased and costs reduced.
Problem definition
Manufacturing tolerances have a significant impact on costs in conveyor technology. Particularly in the case of complex assemblies consisting of various individual parts, tolerance chains arise that require complex mathematical analysis. Pump systems consisting of housing parts, rotor elements, bearing shells, bearing seats, drive shafts and more serve as an example. The decisive requirement for product quality is a specified minimum flow rate, which can be significantly impaired by inaccurate fits, relative play or even friction. Knowledge of these properties alone is often of limited help, as they result from a large number of individual dimensions and combinations of components.
In order to minimize the variations in the actual flow rate achieved, it would theoretically be possible to manufacture each component individually with greater precision. This would reduce the deviations between the individual parts and minimize the error contribution to the overall assembly. However, this approach leads to exponentially increasing production costs and therefore offers little economic benefit for the end product. Modern solutions are needed here.
Objective
The opportunity to examine assemblies for their actual performance in practical tests is used to achieve maximum utilization of the individual parts produced in series. The main objective here is not just the conventional reduction of manufacturing deviations, but rather to achieve the best possible flow rate by cleverly combining the individual parts based on measurement data.
A key challenge is to determine the manufacturing deviations precisely by measuring the actual component dimensions. Due to the complex geometries of the components, this often involves hundreds of individual dimensions. Machine learning is used here to extract relevant information from this extensive amount of data. Understanding which dimensions actually influence the flow rate can have a significant impact on manufacturing costs. The ability to establish a clear link between the measured values and the final product characteristics opens up the prospect of creating a forecast for the output, even if different individual parts show deviations. This promises an exciting opportunity to increase efficiency in manufacturing.
Result
The correlations between the dimensions of the individual parts and the target pump flow rates were convincingly understood. Based on these findings, the machine learning algorithms were equipped with the influence weightings of the individual dimensions. This data is used directly to achieve rapid optimization in production. In this way, crucial tolerances in production can be reduced without leading to unjustifiable additional costs. The theoretical savings from the smaller tolerances can be reinvested in other component areas that only have a minor influence on the pump delivery rate.
In addition, test bench tests are carried out continuously in order to constantly gain new insights into the actual delivery rate. This data basis is continuously integrated into the dynamic training process of the algorithms. The aim is to further improve the forecasting accuracy of the algorithms with regard to the achievable delivery rate. A major advantage is that measured individual parts can be used directly to make predictions and then verify them on the test bench.
Individual parts with significant production deviations no longer have to be rejected from production as a preventative measure. Instead, they can be combined with suitable system components using AI algorithms to ensure the required quality of the assembly.
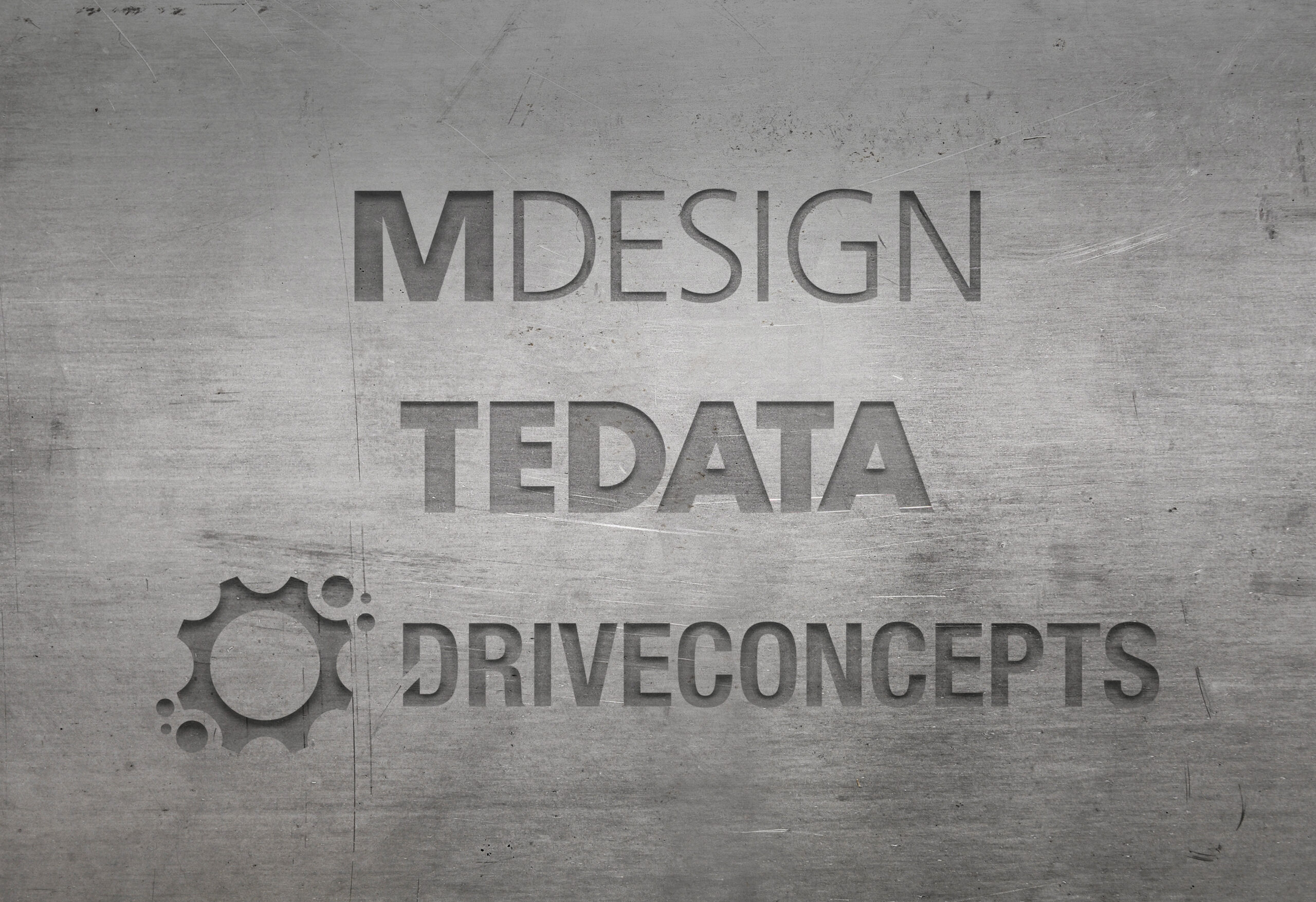
Knowledge for technology
Your strong partners in product development
We support industrial companies on their path to digital transformation. With customized services in simulation, calculation and software development, we promote efficient product development. Put your trust in over 40 years of experience and shape your industrial future.